Simulazione digitale e digital twins: ottimizzazione di tempi, costi e processi aziendali
Nell’era dell’innovazione tecnologica, le aziende di ogni settore affrontano una crescente pressione per ridurre i costi e i tempi, mantenendo al contempo alti standard qualitativi. L’adozione di sistemi di simulazione digitale e digital twins sta rivoluzionando i processi di progettazione, produzione, manutenzione e logistica . Questi strumenti avanzati consentono di anticipare i risultati delle prove fisiche, migliorando l’efficienza e abbattendo i costi associati a cicli iterativi in diverse fasi operative.
La simulazione digitale: un ponte tra teoria e pratica
La simulazione digitale è il processo che replica un sistema o un fenomeno fisico mediante modelli matematici e algoritmi informatici. In pratica, una simulazione digitale crea un modello virtuale di un processo, di un sistema o di un ambiente, permettendo di testare diversi scenari senza i rischi e i costi associati all’uso di macchinari reali. non ancora sviluppati o costruiti.
La simulazione digitale viene utilizzata in vari settori per testare prodotti, sistemi, processi . Applicata nella fase di progettazione, consente di creare modelli digitali in 2D o 3D attraverso software CAD (Computer-Aided Design), che possono includere anche algoritmi matematici per rappresentare parti di un processo o di un prodotto. L’obiettivo principale è ridurre i costi di prototipazione, sostituendo i prototipi fisici con modelli completamente virtuali.
Questi modelli permettono simulazioni altamente realistiche: se un prodotto presenta difetti, è possibile modificare direttamente i dati del modello digitale senza dover creare un prototipo fisico. Un ulteriore vantaggio è la possibilità di testare vari scenari operativi per ottimizzare la qualità e la produttività, individuando la configurazione ottimale prima di passare alla produzione.
Tradizionalmente, le simulazioni sono state utilizzate per valutare i progetti dei sistemi e verificarne la capacità di soddisfare gli obiettivi operativi. Ad esempio, nel settore automobilistico, è possibile testare virtualmente la resistenza strutturale del prototipo di un veicolo in un crash test, individuare i punti deboli e apportare correzioni in modo rapido ed economico.
Digital twins: creare gemelli virtuali
I digital twins (gemelli digitali) ampliano ulteriormente il potenziale della simulazione. Un gemello digitale è più di un semplice modello che integra gli oggetti del mondo reale nel mondo digitale. È una rappresentazione dinamica virtuale di un oggetto fisico, di un sistema o di un processo esistente, che viene continuamente aggiornata con i dati reali. Il gemello digitale comunica in modo bidirezionale e continuo: misura i cambiamenti nel sistema fisico tramite sensori e condivide costantemente le previsioni con il sistema fisico per prendere le decisioni in tempo reale. Aziende come IBM, Siemens e GE stanno già adottando i gemelli digitali.
I gemelli digitali permettono alle imprese di ottimizzare le prestazioni, prevedere problemi futuri e apportare aggiustamenti in tempo reale. Alimentati da tecnologie Industry 4.0 avanzate come sensori IoT (Internet of Things), intelligenza artificiale (AI), machine learning (ML), cloud computing e analisi dei dati, i digital twins sono costantemente connessi a fonti di dati in tempo reale. I sensori integrati negli omologhi fisici inviano dati live al modello virtuale, garantendo la sincronizzazione con la realtà.
Questi gemelli digitali non solo simulano, ma monitorano e ottimizzano le prestazioni durante tutto il ciclo di vita del prodotto. Ad esempio, un impianto industriale dotato di gemelli digitali può prevedere i guasti alle macchine, pianificare gli interventi di manutenzione preventiva e migliorare l’efficienza operativa complessiva. Inoltre, consentono di simulare l’usura dei materiali nel tempo, grazie alla conoscenza delle leggi fisiche, per ottimizzare i tempi di manutenzione o di sostituzione dei componenti.
La modellazione digitale con i digital twins, dunque, è fondamentale per ridurre il rischio di fermi impianto costosi e per massimizzare la produttività. Con i gemelli digitali, le aziende ottimizzano i processi in modo dinamico e continuo, adattandosi rapidamente alle mutevoli esigenze del mercato. Questo approccio permette di simulare non solo i prodotti, ma interi stabilimenti industriali o addirittura sistemi complessi come il corpo umano, aprendo nuove possibilità in ambito medico e ingegneristico.
Confronto tra simulazione digitale e digital twins
SIMULAZIONE DIGITALE |
DIGITAL TWINS |
|
Scopo |
Test e analisi strumentali o predittive di sistemi e fenomeni fisici, formazione avanzata, gestione dei rischi, ottimizzazione dei processi e pianificazione strategica |
Monitoraggio, ottimizzazione e manutenzione predittiva di sistemi e processi in tempo reale |
Dati e interazione |
Utilizzano set di dati predefiniti e potrebbero non incorporare aggiornamenti in tempo reale. L’interazione avviene prima della simulazione, impostando dati e parametri statici e monodirezionali, al fine di testare condizioni e scenari diversi e osservare i risultati |
Il flusso dei dati tra il sistema fisico e il gemello digitale è continuo, bidirezionale e in tempo reale, per aggiornare continuamente il modello virtuale. Il digital twin permette l’interazione con il modello per testare dinamicamente diversi scenari |
Investimento |
E’ contenuto per la facile configurabilità, l’assenza dei dati in tempo reale e di una integrazione continua con il sistema fisico |
E’cospicuo perché, per rappresentare efficacemente il sistema fisico, occorre integrare i dati dei sensori con l’analisi in tempo reale e l’AI |
Ciclo di vita |
In generale l’uso della simulazione digitale avviene per un breve periodo del ciclo di vita, al fine di fornire i risultati voluti in scenari specifici |
I gemelli digitali mantengono una relazione continua con le loro controparti fisiche, lungo tutto il ciclo di vita. L’uso è per periodi medio-lunghi e il gemello evolve di pari passo con il sistema fisico replicato |
Creazione del modello |
I modelli di simulazione possono variare in complessità, dai semplici modelli statistici a rappresentazioni complesse e dettagliate |
I gemelli digitali richiedono modelli multistrato in grado di replicare le controparti del mondo reale |
Applicazioni della simulazione digitale e dei digital twins
A partire dalle fasi di progettazioni e proseguendo nelle fasi di industrializzazione e produttive, e applicazioni della simulazione digitale e dei digital twins nei processi aziendali offrono vantaggi tangibili in termini di ottimizzazione di tempi, costi, qualità e sostenibilità.
A seconda delle esigenze si possono applicare singolarmente o in modalità integrata. Vediamo insieme le applicazioni nei due approcci per alcuni settori chiave.
Applicazioni della simulazione
Meccanica
Attraverso simulazioni di usura, attrito e sollecitazioni si ottimizzano i componenti meccanici, come ingranaggi o motori. Questo permette di ridurre i costi di manutenzione e migliorare le prestazioni dei macchinari industriali.
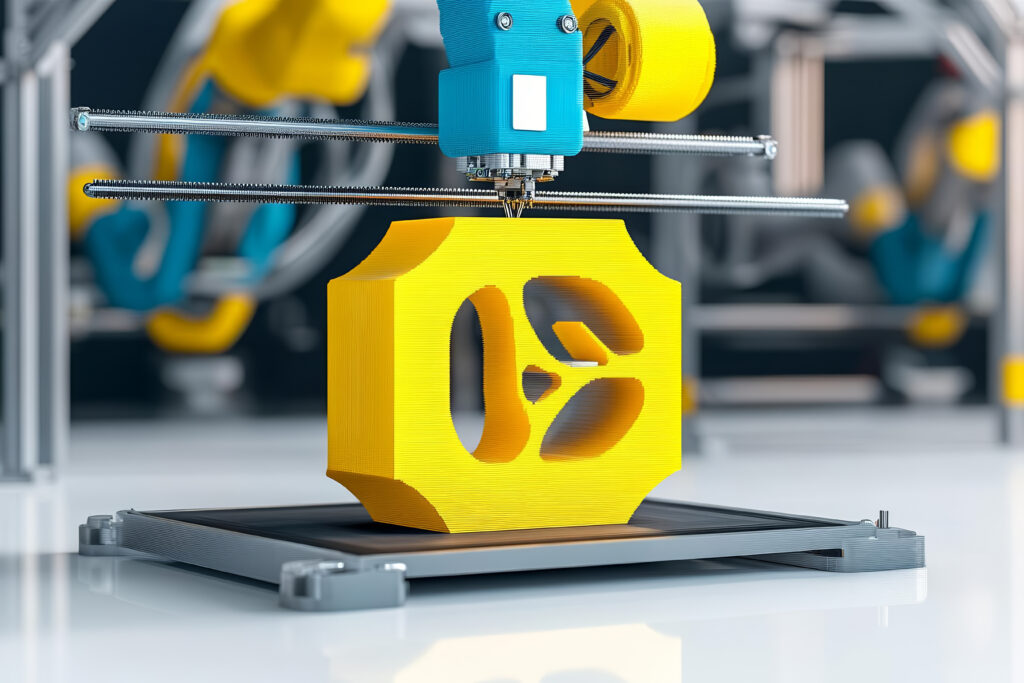
Plastica
Con la modellazione del processo di stampaggio a iniezione si riducono i difetti nei pezzi prodotti, si ottimizza l’uso dei materiali e si migliora la qualità dei prodotti finiti.
Applicazioni dei digital twins
Aerospace
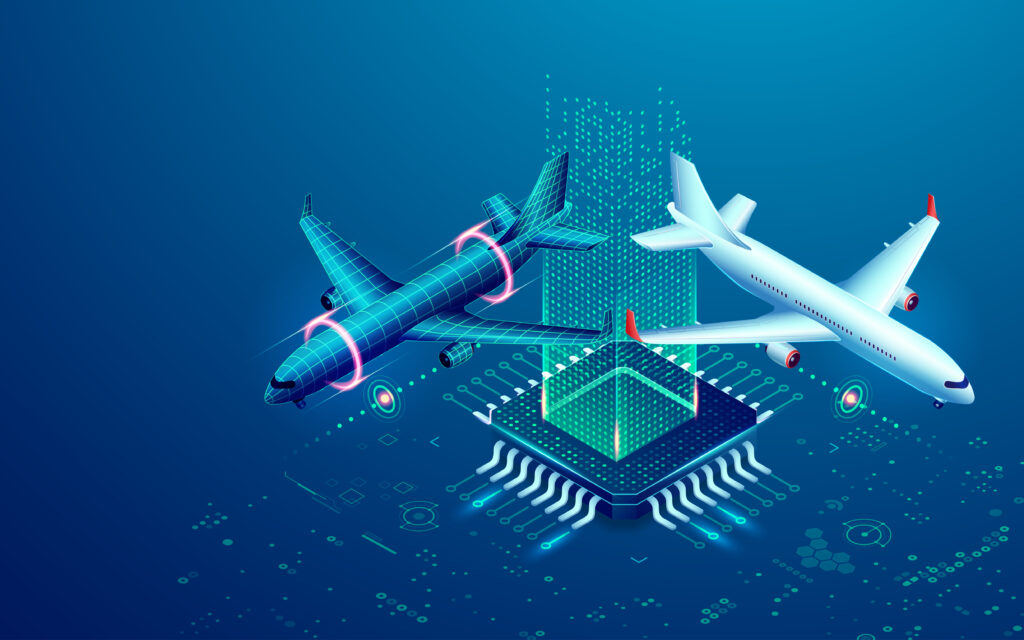
Airbus usa i digital twins sull’intera flotta di aeromobili per monitorare i dati di volo in tempo reale, mantenere condizioni ottimali e anticipare i problemi prima che si manifestino. Mediante le repliche virtuali dei suoi aerei, Airbus può simulare scenari diversi, valutare le prestazioni e prendere decisioni informate. L’integrazione della tecnologia del gemello digitale da parte di Boeing nella progettazione e produzione degli aeromobili è un esempio delle sue potenzialità. In questo caso, è stato utilizzato un gemello digitale per simulare le parti di un aereo e analizzare come diversi materiali si comporteranno durante l’intero ciclo di vita dell’aeromobile. Grazie a questi calcoli, Boeing è riuscita a ottenere un miglioramento del 40% nella qualità di alcune parti progettate.
Automotive
Tesla è all’avanguardia nell’uso dei digital twins per la progettazione, i test, e l’ottimizzazione dei suoi veicoli elettrici, prima ancora che arrivino sulla linea di produzione. Utilizzando le simulazioni con i digital twins, Tesla ha migliorato la qualità dei prodotti, ridotto il tempo di sviluppo e snellito i processi produttivi.
Applicazioni miste della simulazione digitale e dei digital twins
Manifattura
Un produttore di automobili che desidera migliorare l’efficienza della linea di assemblaggio può utilizzare i gemelli digitali per creare una replica del processo produttivo attuale. Integrandoli con la simulazione, è possibile testare cambiamenti come la riorganizzazione delle stazioni di assemblaggio o l’introduzione di bracci robotici. Così si prevede l’impatto di questi cambiamenti sulla produzione, sulla qualità del prodotto e sulla sicurezza dei lavoratori, assicurando che le modifiche siano in linea con i risultati desiderati.
Energia
Con la simulazione di impianti eolici e fotovoltaici si ottimizza la produzione e si riducono i costi di manutenzione. General Electric (GE) sfrutta la tecnologia dei gemelli digitali per prevedere i guasti e ridurre i tempi di fermo delle turbine eoliche. Analizzando costantemente i dati provenienti da vari componenti della turbina, GE è in grado di ottimizzare i suoi processi, aumentare la produzione di energia e prolungare la vita delle sue attrezzature.