What is a digital biogas production plant
Digital biogas plants incorporate advanced digital technologies to optimize biogas operation and production. This includes the use of sensors, data analysis, and software solutions to monitor and control the anaerobic digestion process in real time. The synergy between digital innovation and environmental sustainability is a key step toward a greener and more efficient future.
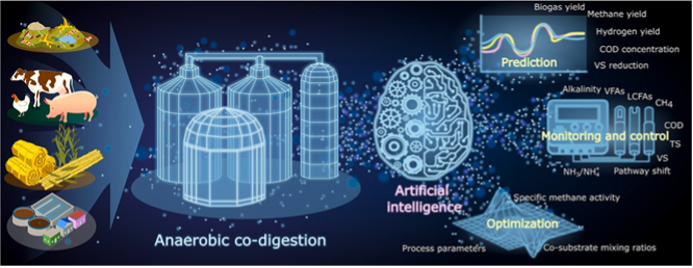
Sensors provide sufficient data to find correlation between parameters and create operational models that enable predictive and flexible operation of biogas plants.
This prevents failures and achieves production based on demand and available resources. Artificial intelligence (AI) and machine learning (ML) help optimize important process parameters such as co-sustrate mixing ratio (Palma-Heredia et al., 2021), biogas yield (Kainthola et al., 2020), retention time, temperature, hydraulic retention time (HRT), C/N ratio, and pH. Siemens, GE and several technology startups are already implementing AI-based solutions in biogas plants around the world.
For example, Siemens’ “Mind Sphere” platform enables plant operators to monitor and control operations in real time using data analytics via AI, which significantly increases efficiency and reduces costs.
Characteristics of digital biogas production plants
Optimization of raw materials
- Digital systems analyze the composition and characteristics of different feedstocks, enabling the plant to use the most efficient mixture to achieve the highest biogas production yield.
- By carefully selecting and combining raw materials, digital plants reduce waste and make the best use of available resources, improving overall sustainability.
Automated process control
- Based on real-time data, digital control systems can make automatic adjustments to optimize the fermentation process. This includes controlling raw materials, adjusting temperature and changing the mixing patterns of the contents within the anaerobic digester.
- Automation allows the plant to self-regulate even under dynamic conditions, such as during fluctuations in gas production or malfunctions, without manual intervention.
Advanced product gas control
- Digital biogas plants continuously analyze and monitor the quality and composition of the gas produced (methane, carbon dioxide, hydrogen sulfide) to ensure that it meets quality standards for use or sale.
- If the quality of the gas produced fluctuates, digital control systems make real-time adjustments, helping to maintain consistent, high-quality biogas production.
Energy efficiency and consumption management
- Digital systems monitor plant energy consumption and identify areas where energy efficiency can be improved. For example, controlling the timing of energy-intensive processes or using energy only when biogas production is optimal. Some plants are equipped with smart grid technologies, which enable them to contribute to the grid during peak periods and optimize energy consumption during periods of low demand.
Predictive maintenance and plant status monitoring
- By analyzing plant performance data, Machine Learning algorithms predict when different components (e.g., mixers, agitators, pumps, compressors, heat exchangers) need maintenance. This prevents unexpected downtime and reduces repair costs.
- Sensors monitor the condition of the machines, providing alarms about problems such as vibration, wear, or overheating. Maintenance programs are optimized based on the actual use of the plant and its actual operating conditions of operation.
Data collection and real-time monitoring
- Digital biogas plants are equipped with IoT devices and sensors that collect real-time data on temperature, pH levels, gas composition, pressure, flow rate, and other crucial parameters.
- IoT devices transmit data to a centralized platform, enabling continuous monitoring and control. Operators can view data remotely via a dashboard accessible on computers or mobile devices.
Remote monitoring and control
- Operators can monitor and control the plant remotely, via a secure Internet connection. This is particularly advantageous for plants located in remote areas or to minimize the presence of personnel at the site.
- Remote access enables timely response to operational problems or emergencies, reducing downtime and ensuring smooth plant operation.
Conclusion
The synergy between digital technologies and green solutions is transforming the energy landscape, making biogas plants not only more efficient but also more sustainable. The integration of advanced sensors, artificial intelligence and automation is optimizing plant management, reducing operating costs, increasing energy production and minimizing environmental impacts.
Smart biogas production facilities not only meet the energy challenges of the present, but also represent a cornerstone for a greener, more efficient, and more resilient energy future. As digital technologies continue to develop and green strategies expand, smart biogas production becomes a key driver for the transition to a circular economy and low carbon footprint.